Whether you’re an auto repair shop owner or a customer, word of mouth is the best way to determine if you’ve found an honest mechanic. Ask your friends and family about their experiences.
Look at employee turnover and the length of time that employees have worked in the shop. High turnover can be a sign that employees aren’t treated well. Contact Juanito’s Auto Body now!
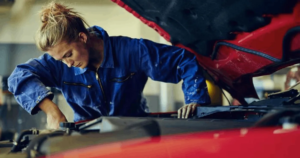
MIG welding is a widely used manufacturing and fabrication process for joining metal parts. It’s known for its speed and teeny tiny learning curve (there isn’t one). Here’s what you need to know about this welding technique, along with some tips and tricks for getting the best results.
In MIG welding, a constant voltage power supply creates an electric arc between the workpiece and a consumable wire electrode filler. This arc melts the base metals and forms a weld pool. Meanwhile, an inert gas—typically a mixture of argon and carbon dioxide—shields the molten weld puddle from atmospheric contaminants, ensuring that your finished weld will be strong and clean.
Before you start welding, it’s important to prepare the workpiece by removing any dirt, oil, or other debris. Then, make sure your welding machine is set up according to the specific material thickness and wire diameter. Lastly, you’ll need to select the correct shielding gas for the type of metal you’re working with.
The most commonly used shielding gas for MIG welding is a 75% argon 25% CO2 mixture—known commercially as C25. However, you can also use straight CO2 or a non-reactive gas like helium. This shielding gas is crucial because it prevents the welded metal from reacting with oxygen in the atmosphere, causing it to oxidize and deteriorate over time. If the oxidation isn’t removed, your weld will be weak and unreliable.
TIG (Tungsten Inert Gas) Welding
Tungsten inert gas welding, also known as gas tungsten arc welding (GTAW), is a type of welding responsible for securing some of the world’s most crucial equipment and machinery. Its ability to produce cleaner welds with superior corrosion resistance makes it a favorite for fabricating and repairing aluminum parts. TIG welding also produces extremely ductile welds, making it ideal for applications that require pinpoint fabrication.
TIG welding involves using an electric current to heat and melt a metal and create a weld. An electrode — often made of tungsten alloyed with various metals to increase its melting point — is then placed in the center of this process and arc. An inert shielding gas like argon or helium is used to keep the arc and weld puddle safe from contamination.
While TIG welding can be done on a variety of different metals, it is particularly well-suited to aluminium and its alloys. It can even be used on cast iron, though a special coating of activated flux is required.
The main drawback of TIG welding is its slower deposition rate compared to other welding processes, making it difficult to work with on large projects outside of a controlled environment. It can also be challenging to use on uneven or rusty surfaces due to the need for extra preparation before starting the welding process. This is because rust must be completely removed before TIG welding can be effective.
Paintless Dent Repair (PDR)
PDR is a popular and cost-effective alternative to traditional body repair methods. It is non-invasive, fast, and preserves your vehicle’s factory paint. It is also an insurance-friendly option, so your out-of-pocket costs may be less than your deductible.
With PDR, technicians use industry-grade tools to massage the dent back into its original shape. The tools are often customized to fit your car’s make and model, allowing the technician to access the hidden backside of the damaged panel. This technique can fix a variety of dents and creases, including door dings, hail damage, and body/feature line dents.
The longer metal stays in a distorted state, the harder it is to return it to its original shape. This is why it is important to address damage as soon as possible.
To perform a PDR, the technician first assesses the damage to determine whether it is appropriate for this method. They will take into account factors such as the size, depth, and location of the dent. The technician will then gain access to the damaged area by removing parts such as panels or lights. Once they have accessed the dent, they will apply gentle pressure to massage the metal back into its original form. Some techniques that the mechanics might use include glue pulling (a process where hot glue is applied to tabs and then pulled out), or they might use a metal rod from behind to push out the dents.
Metal Bonding
Bonding metal to metal is an important method for the body shop. It provides a fast and cost-effective alternative to welding and rivets. It also allows for the vehicle to be reassembled in the same manner as it was originally manufactured, maintaining the original engineering specifications. This system also eliminates the need for holes which are prone to corrosion and loosening over time.
The adhesive system is especially useful when working with aluminum panels and dissimilar metals, and it allows for a quick and easy repair procedure. It is a very common method of repair when working on newer cars with aluminum panels, including Ford F150 trucks. The adhesive system is an excellent choice for repairing structurally significant components as it can absorb a great deal of crash energy, providing better protection for the vehicle occupants.
Using adhesives in the collision repair industry requires proper panel preparation and cleaning to ensure a high quality and long-lasting bond. In addition, it is recommended to use personal protective equipment to ensure safety and compliance with any applicable regulations.
In choosing an adhesive, shops should look for products that meet OEM specifications for strength and durability, as well as those with low odors and easy gun application. The de-clamping time of the product is also an important consideration, as it impacts technician productivity. AA-BOND 2123 is a versatile steel metal/epoxy adhesive formulation developed for modern industrial repair, casting and bonding applications requiring a steel-like or cast iron finish.
Painting
If you have a dispute with an auto repair shop, it’s always best to try and resolve the issue informally. Speak with management, and provide details about the problem. Keep records of your discussions, as well as copies of any work orders or invoices. If you are unable to reach an agreement, contact your local consumer group for assistance. They can help you contact a neutral mediator to settle the dispute. A mechanic’s occupation is expected to grow as people continue to drive their cars longer and replace them with newer models. These trends make it important to maintain a strong and reputable shop.